News / Tech News |
More than flying cars: eVTOL battery analysis reveals unique operating demands
Researchers at the Department of Energy’s Oak Ridge National Laboratory are taking cleaner transportation to the skies by creating and evaluating new batteries for airborne electric vehicles that take off and land vertically.
The operating phases of an eVTOL need varying amounts of power; some require the battery to discharge high amounts of current rapidly, reducing the distance the vehicle can travel before its battery must be recharged. Photo: Andy Sproles/ORNL, U.S. Dept. of Energy
These aircraft, commonly called eVTOLs,range from delivery drones to urban air taxis. They are designed to rise into the air like a helicopter and fly using wing-borne lift like an airplane. Compared with helicopters, eVTOLs generally use more rotors spinning at a lower speed, making them both safer and quieter.
The airborne EVs aren’t just flying cars, and ORNL researchers conclude that eVTOL batteries can’t just be adapted from electric car batteries.
So far that has been the dominant approach to the technology, which is mostly in the modeling stage. ORNL researchers took a different tack by evaluating how lithium-ion batteries fare under extremely high power draw.
“The eVTOL program presents a unique opportunity for creating a brand new type of battery with very different requirements and capabilities than what we have seen before," said Ilias Belharouak, an ORNL Corporate Fellow who guides the research.
Researchers are developing new energy-dense materials, learning how these materials degrade under extreme conditions, and developing battery control systems.
“This requires us to answer questions about the interplay of battery safety, cycle life and stability at high temperatures, while balancing the need for short bursts of high power with energy reserves for longer-range flight,” Belharouak said.
The first major takeaway from an extensive eVTOL research project underway at ORNL is that the power and performance demands for eVTOL batteries can significantly reduce their longevity and durability.
Unlike electric vehicle batteries, which typically drain at a steady rate, eVTOL batteries need varying amounts of power for flight stages such as climbing, hovering and descent, with some phases requiring high bursts of power.
“Now we know more about what is required of the eVTOL battery, we’ll need to engineer systems differently to achieve that,” said ORNL lead researcher Marm Dixit.
“Our focus is fundamental: What happens to the materials under these specific loads and operating conditions? We are trying to figure out the limitations of the battery chemistry we have now, and then tune the battery to bridge that gap.”
The ORNL team made lithium-ion batteries at the DOE Battery Manufacturing Facility located at ORNL and ran them through simulated climb stages of eVTOL aircrafts.
Scientists studied what happened inside the battery during cycling – including how much energy was rapidly accessible during the demanding takeoff phase – then tested the battery materials afterward for corrosion and other chemical or structural changes.
Systematic investigation linking actual flight profiles to real-time physical battery operation is rare. However, it is key groundwork for developing new battery chemistries to achieve safe flight performance.
The study incorporates testing of a new ORNL-developed electrolyte — a material through which electrodes exchange ions — against the current state-of-the art version used in lithium-ion batteries.
Using the eVTOL mission profiles, the ORNL electrolyte performed better, retaining more capacity during the most power-demanding flight phases.
These results demonstrate the need for diversifying how battery performance is measured, Dixit said. “Your battery is not just capacity at the end of 1,000 cycles.
It’s what’s happening within a cycle that tells you whether your system is going to work or crash. And the stakes are much higher here because you’re asking how safe it is to go up in the air. This is a question we don’t know the answer to — yet.”
Members of the research team are working on further improvements to the electrolyte and other battery components as they push the engineering limits for battery power, payload and safety.
Recent experiments involved collecting real-world data from drone flights over the lab’s campus, then using that information to develop a customized profile of the load and draw on the battery. Batteries made at ORNL were then run through same cycles.
YOU MAY ALSO LIKE

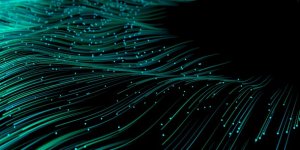

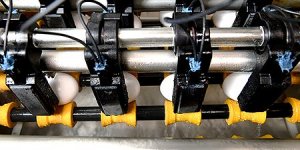








